Page 7 of 10
Posted: Mon Mar 16, 2015 9:14
by FDEEZ
Shadowden wrote:Does your new job involve welding or are you doing it as a hobby? I have gathered that lanthanated tungsten can be used more universally/easily. Kind of jealous you get to TIG a lot. I spent an hour playing with one and liked it, but not nearly enough time to get good at it. If I read closer, I would have noticed I am not seeing the pictures, so will check it all out later.
Anything that does NOT involve computers/networks is a hobby to me. Otherwise, I consider it work. Fiddling around with the car...and now welding...are just things to relax my mind and get me away from a computer screen.
I do more cyber type stuff at work. My new job involves developing cyber strategies at enterprise levels. Not sure I enjoy it, but it pays the bills. It's funny though...despite being a cyber geek, my car's PCM is completely foreign to me
Regarding the 2% lanthanated, I previously used ceriated tungsten...but got mixed results. I blame it more on operator error than on the tungsten though. Hopefully I'll get better results with more seat time. My current tig setup sure makes welding more enjoyable.
Posted: Mon Mar 16, 2015 9:14
by Shadowden
If you ever have a big project to do and need an extra set of hands, I'd be willing to help out. I'm in the same boat. I drive a desk 8-9 hours a day, so I really like the opportunity to get my hands dirty with the car or welding. I haven't been on the mig enough recently so the welds are not as pretty as I would like. I have a friend helping me hook up 220 in the garage, so I am hoping the extra power will get the weld hot faster, and keep it nice and flat on butt or T welds. My mig is millermatic 211.
Posted: Mon Mar 16, 2015 9:14
by Saul_Good
Going to stitch weld chassis soon? Damn all this fabrication going on I need to learn a trade!
Posted: Tue Mar 17, 2015 9:14
by FDEEZ
Shadowden wrote:If you ever have a big project to do and need an extra set of hands, I'd be willing to help out. I'm in the same boat. I drive a desk 8-9 hours a day, so I really like the opportunity to get my hands dirty with the car or welding. I haven't been on the mig enough recently so the welds are not as pretty as I would like. I have a friend helping me hook up 220 in the garage, so I am hoping the extra power will get the weld hot faster, and keep it nice and flat on butt or T welds. My mig is millermatic 211.
Thanks for the offer to help. The next big project will probably be fabricating a cage for the car...but it'll be a while before I go down that chromoly road.
That Millermatic 211 you have is a beast. 99% of the time you won't ever need 230V for your welder, but it's nice to have the extra power the 1% of the time you do need it. I can't be more impressed with the quality/technology of Miller machines. I've welded some pretty thick stuff on 110V with my Miller...and have yet to blow a breaker (knock on wood).
Saul_Good wrote:Going to stitch weld chassis soon? Damn all this fabrication going on I need to learn a trade!
At this point in time, I wouldn't trust my welds on anything structural or load bearing. But I'll let you know when I "think" I am...you can be my guinea pig :-) Also, there's a debate out there on the pros/cons of stitch welding a chassis. One team says it actually weakens the integrity of the car. I'm not sure what side I'm on...as some cars come stitch welded from the dealership.
Posted: Mon Mar 23, 2015 9:14
by FDEEZ
FDEEZ wrote:
I'm most likely going to duplicate 99% of everything done to that car except:
- Full roll cage...mine will probably be a 4-point "street bar" configuration
- Wing
- Lexan front window
- Fiberglass doors
Other than those, everything else on that car is on my wishlist. One of the things I like about that car is the Honda S2000 ABS setup. I was considering switching to a BMW M3 ABS setup...but the S2000 seems more within my budget.
I'm going to have to retract my above statement. I bought fiberglass doors from the exact same manufacturer of the doors on the red car.
They just arrived:
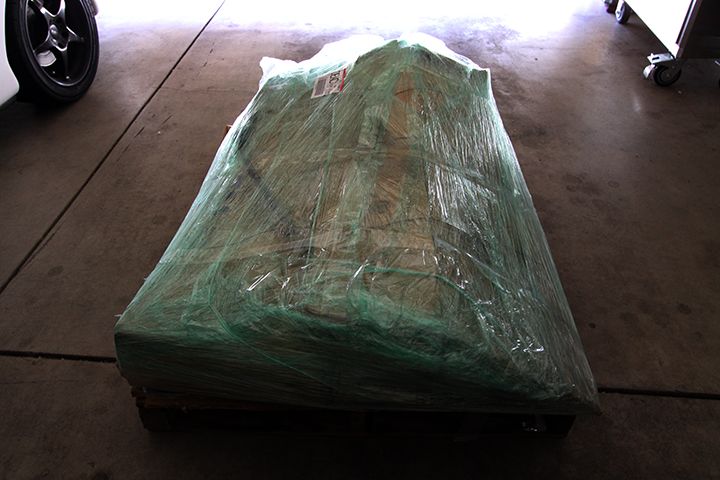
These are definitely going to need some major body work and TLC to be decent enough to put on my car. They are far...and I mean far from perfect...but you get what you pay for...and these were cheap. At least they're light.
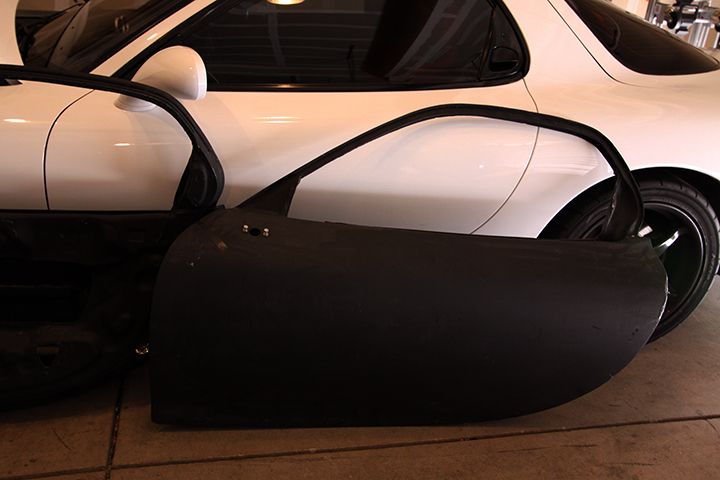
My rear flares also arrived. Just hung them on the car to get a feel of how they may look like when installed.
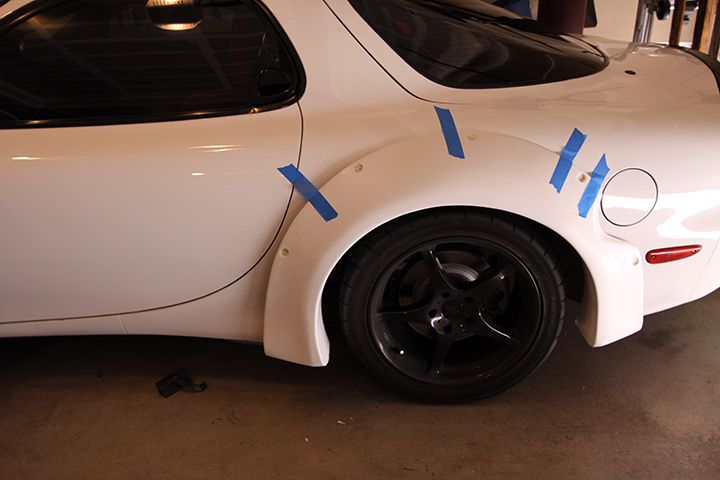
I haven't decided on whether I'm going to mold them into the body or rivet them in place.
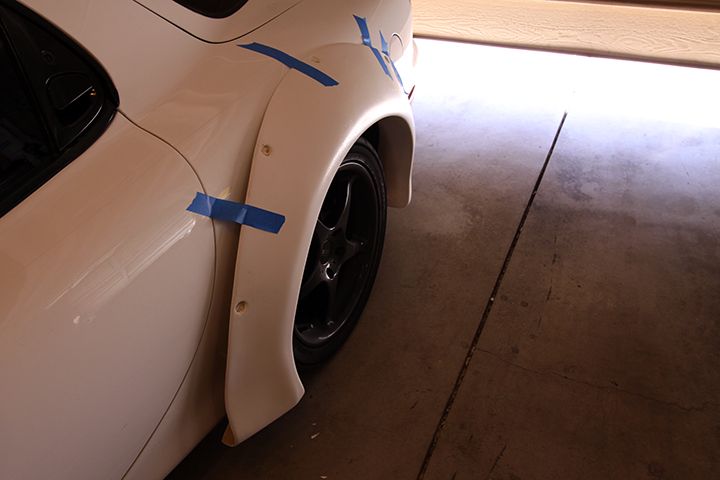
Since the car is running perfectly, performs well, and looks good as is...I'm extremely timid on the thought of tearing the car apart to make it more un-streetable. Additionally, I'm not sure if I'll have the courage to cut open the perfect rear body to install those flares. Much to consider.
Posted: Tue Mar 24, 2015 9:14
by Shadowden
I think the stitch welding of the chassis is a problem when so much heat/material is added by a poor weld job. The sheet metal near the weld looses some of its elasticity and just tears. I think that problem is more prevalent with migs and their really rigid welds too. If you do a good job with a tig (or even stick), it wouldn't be a problem I don't think. If a good weld is made with a mig, I think ti is fine too, but it can just be goobered on there (so to speak).
Posted: Tue Mar 24, 2015 9:14
by VRx8
I was going to do Pettit flares but decided not to. Just couldn't get myself to cut the quarter panels.
Posted: Thu Mar 26, 2015 9:14
by FDEEZ
Shadowden wrote:I think the stitch welding of the chassis is a problem when so much heat/material is added by a poor weld job. The sheet metal near the weld looses some of its elasticity and just tears. I think that problem is more prevalent with migs and their really rigid welds too. If you do a good job with a tig (or even stick), it wouldn't be a problem I don't think. If a good weld is made with a mig, I think ti is fine too, but it can just be goobered on there (so to speak).
I'm not sure I'd have the mental/physical endurance to tig stitch-weld a chassis. That's some serious dedication right there.
VRx8 wrote:I was going to do Pettit flares but decided not to. Just couldn't get myself to cut the quarter panels.
I'm not sure I'll be able to dissect my panel either. But to get traction, it's either I run slicks or wider wheels...or slicks on wider wheels for max performance. For what I have, I'm not putting all the power to the ground (and I definitely don't want to decrease my power either). The last option, however, is to electronically get traction via traction/stability control. But that would require replacing my RoadRunner ECU with something even more expensive...which I don't want to do.
Posted: Fri Mar 27, 2015 9:14
by Shadowden
I like the flares. I like when they are molded in better than riveted, especially with as clean as the rest of your car is.
Posted: Fri Mar 27, 2015 9:14
by Saul_Good
Before he sold it, my buddy molded his. V8RX7 w/Rear mount turbo

Posted: Fri Mar 27, 2015 9:14
by RX-7 Chris
I like the riveted look better. Plus if one ever gets damaged, you can just replace it and not have to repaint 1/4 of the car. Also you would have to repaint the car if you molded them.
Posted: Fri Mar 27, 2015 9:14
by lOOkatme
I vote to not install it. roll the fenders, get some custom wheels with great offsets for what you want and you can easily run wide tires. if you need help with offsets let me know.
Posted: Wed Apr 01, 2015 9:14
by FDEEZ
Attempting to get used to this whole welding thing. Still not pretty, but better than before. Hopefully by the end of April I'll have straighter lines, consistently spaced beads, and no craters at the end of the welds. Slowly getting there though...
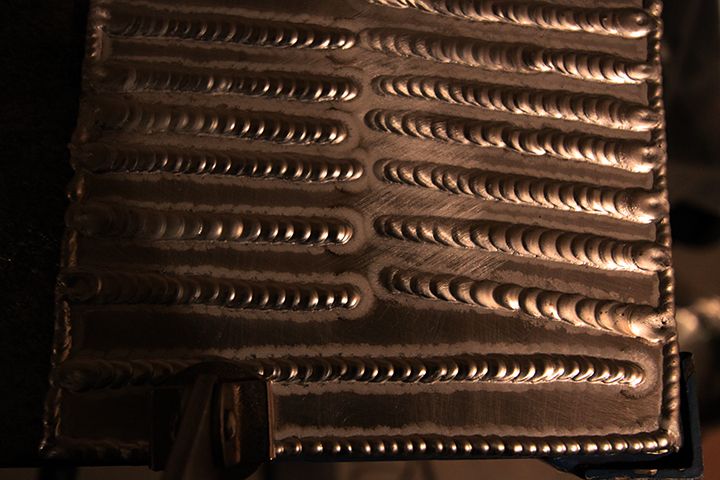
Posted: Wed Apr 01, 2015 9:14
by Saul_Good
That's it! I need to get in on this welding trip
Posted: Thu Apr 02, 2015 9:14
by speedjunkie
Yeah me too. Those look great!